Production of colored PET plastic sheet rolls
Colored PET (Polyethylene Terephthalate) plastic sheet rolls are produced through a series of well-defined processes that include polymer synthesis, extrusion, coloring, and finishing. Here’s a detailed overview of the process:
1. Polymer Synthesis:
PET is synthesized through a polycondensation reaction between terephthalic acid (or its dimethyl ester, dimethyl terephthalate) and ethylene glycol. This process forms long chains of the PET polymer, which are then pelletized for further processing.
2. Drying:
PET pellets are hygroscopic, meaning they absorb moisture from the air. Before processing, they must be thoroughly dried to avoid hydrolytic degradation during melting. This is usually done in a drying hopper at temperatures around 160-170°C.
3. Extrusion:
The dried PET pellets are fed into an extruder, where they are heated and melted. The molten PET is then pushed through a flat die to form a continuous sheet.
4. Coloring:
Color can be added to the PET sheet either during polymer synthesis or more commonly during the extrusion process. This is done by adding masterbatch colorants (concentrated pigments) or liquid colorants to the PET melt. The colorants are mixed thoroughly with the PET to ensure uniform coloration.
5. Casting:
The molten PET is extruded through the flat die onto a cooling roll or water-cooled casting roll. The cooling roll solidifies the PET into a sheet form. The thickness of the sheet is controlled by adjusting the gap of the die and the speed of the cooling roll.
6. Orientation (Optional):
In some cases, the PET sheet is subjected to a biaxial orientation process, which involves stretching the sheet in both the machine direction (MD) and the transverse direction (TD). This enhances the mechanical properties, clarity, and barrier properties of the PET sheet.
7. Finishing:
The PET sheet is then wound onto rolls for further processing. Additional steps such as corona treatment can be applied to improve surface properties for printing or lamination. The edges of the sheet may be trimmed to ensure uniformity and the rolls are inspected for quality.
8. Quality Control:
Throughout the process, quality control measures are in place to ensure the final PET sheet meets required specifications. This includes checking for thickness, color uniformity, mechanical properties, and surface finish.
9. Slitting and Rewinding:
The large rolls of PET sheet are slit into narrower rolls according to customer specifications. These narrower rolls are then rewound and packaged for shipment.
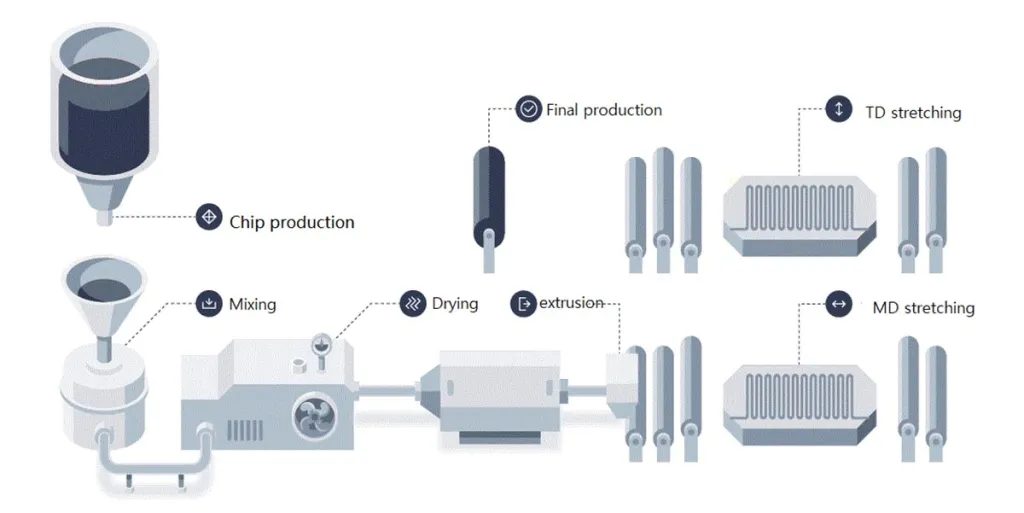
What is colored PET plastic sheet rolls?
Colored PET (Polyethylene Terephthalate) plastic sheet rolls are thin, flexible sheets made from PET that have been dyed or pigmented to achieve various colors. PET is a type of plastic known for its strength, durability, and resistance to moisture, chemicals, and UV light. These colored sheets are used in a variety of applications due to their versatile properties.
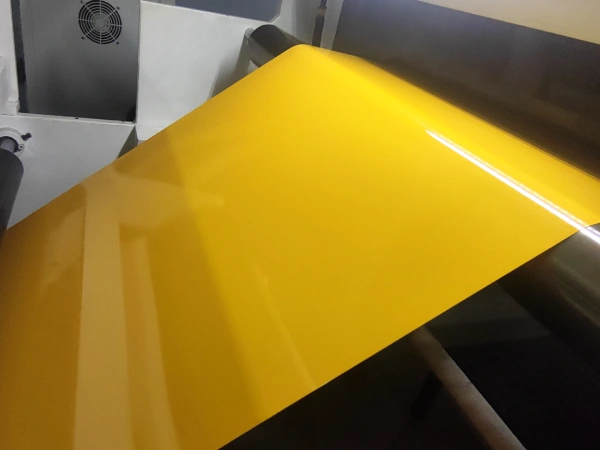
Key Features of Colored PET Plastic Sheet Rolls
1. Durability: PET is known for its toughness and resistance to impact, making it suitable for many industrial and commercial uses.
2. Transparency and Clarity: Although these particular sheets are colored, PET can be produced with high transparency and optical clarity.
3. Chemical Resistance: PET is resistant to a wide range of chemicals, which makes it suitable for packaging and protective applications.
4. Thermal Stability: PET can withstand various temperatures, providing stability in different environmental conditions.
5. Lightweight: Despite its strength, PET is relatively lightweight, which can be beneficial for many applications.
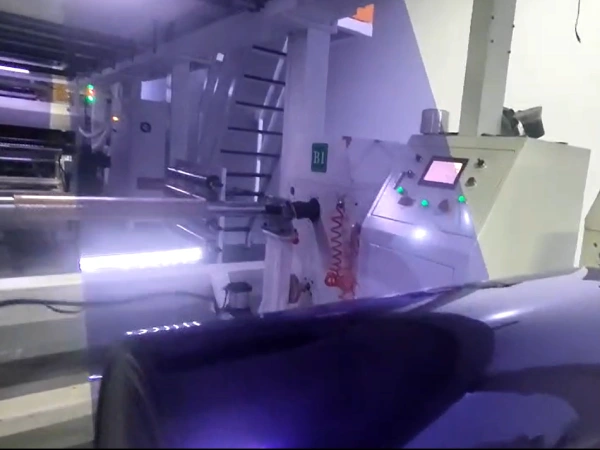
Benefits of Colored PET Plastic Sheet Rolls
1. Aesthetic Appeal: The addition of colors can enhance the visual appeal of products.
2. Customizability: Available in a wide range of colors, allowing for customization based on specific needs and branding requirements.
3. Functional Properties: Combines the aesthetic benefits of color with the functional properties of PET plastic, such as durability and resistance.
Application of PET Plastic Sheet Rolls
Colored PET plastic sheet rolls have a wide range of applications and are suitable for packaging a variety of products. Here are some common application areas:
1. Food packaging: Colored PET plastic sheet rolls is often used to package a variety of foods, such as beverage bottles, food trays, candy packaging, and food cover films, due to its bright colors and excellent transparency and barrier properties.
2. Electronic product packaging: Colored PET plastic sheet rolls has excellent antistatic and protective properties, and is suitable for packaging electronic components, batteries, mobile phone accessories and other products.
3. Medical packaging: Colored PET plastic sheet rolls is non-toxic and odorless, meeting the strict requirements of pharmaceutical packaging, and is often used for pharmaceutical packaging, medical device packaging, and sanitary product packaging.
4. Daily chemical product packaging: Colored PET plastic sheet rolls has strong chemical resistance and is suitable for packaging cosmetics, washing products, care products, etc.
5. Industrial packaging: Colored PET plastic sheet roll is tough and durable, and is often used to package a variety of industrial products, such as auto parts, mechanical parts, and building materials.
6. Gift packaging: Since Colored PET plastic sheet rolls can be customized in a variety of colors and patterns, it is often used to make gift boxes, gift bags, and other decorative packaging materials.
These are just some of the applications of Colored PET plastic sheet rolls, which are widely used in packaging needs in various fields due to their versatility and excellent performance.
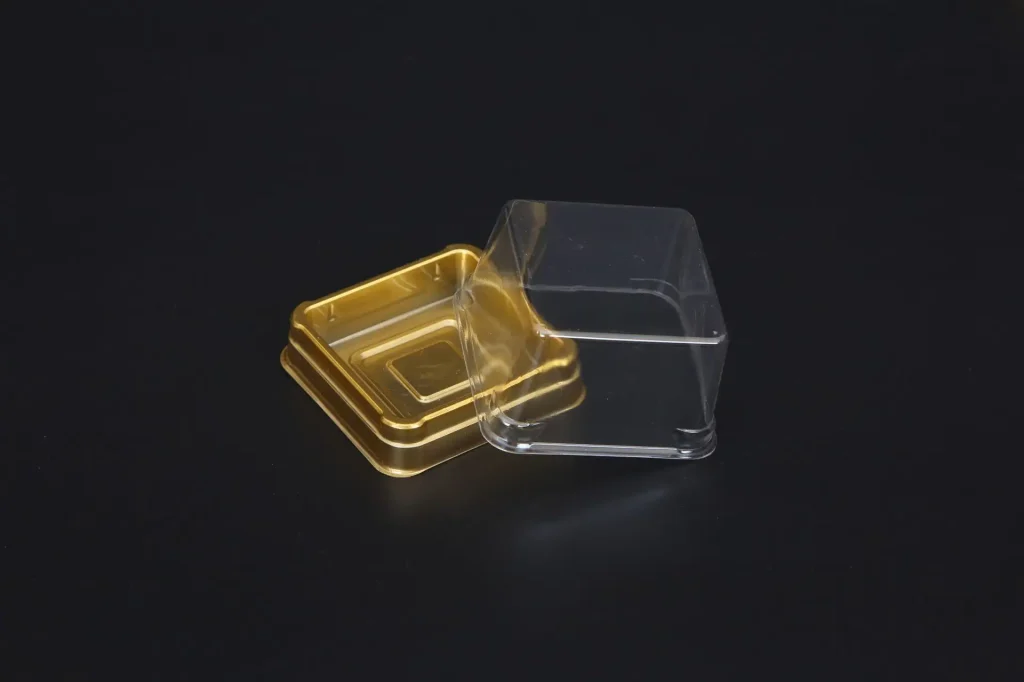
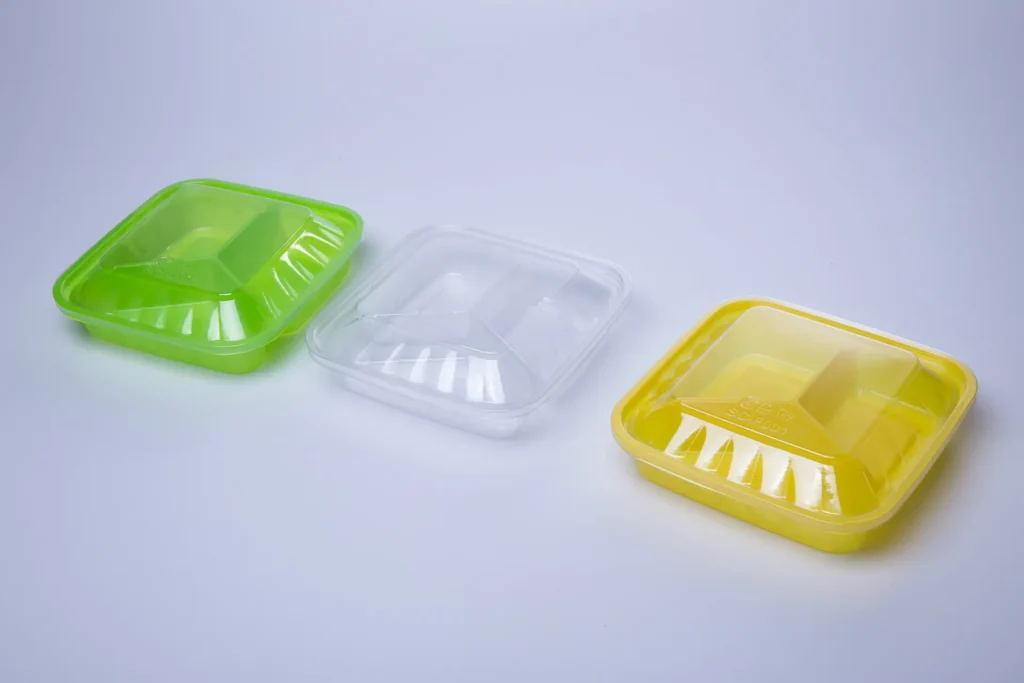
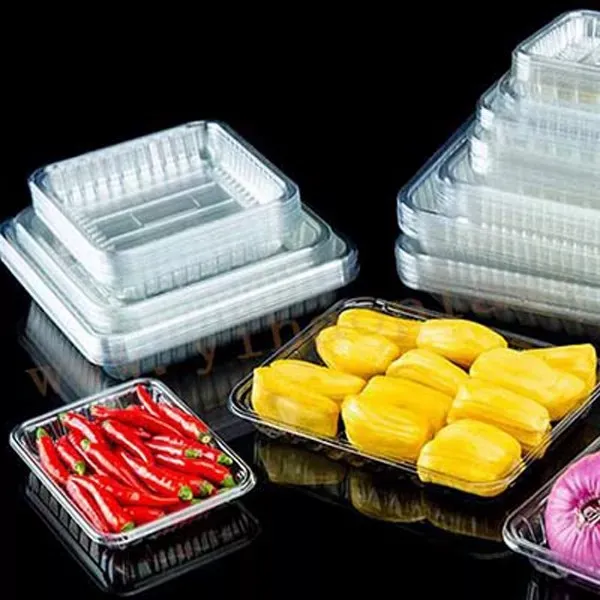
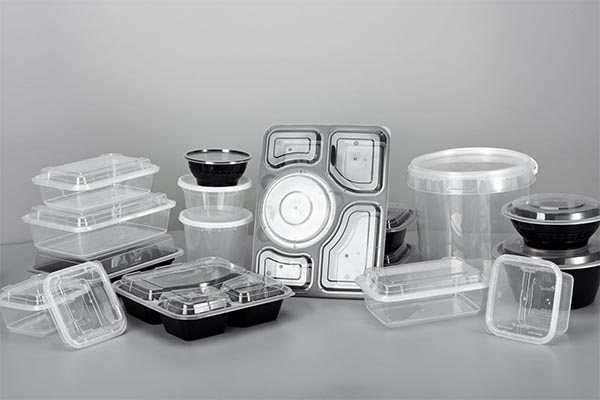
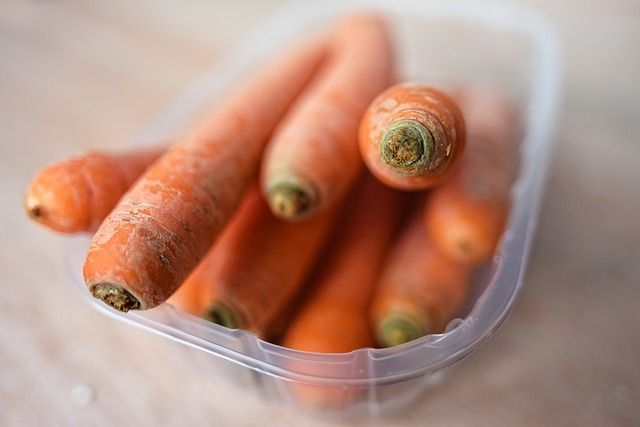
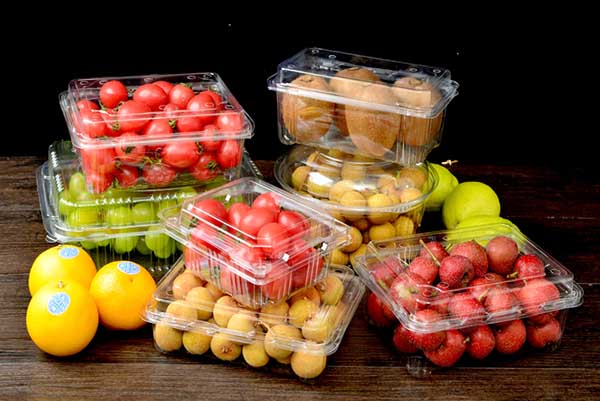
The difference between colored PET plastic sheet rolls and transparent PET plastic sheet rolls
Color: colored PET plastic sheet rolls have color, while transparent PET plastic sheet rolls.
Transmittance: The transmittance of colored PET plastic sheet roll is lower than that of transparent PET plastic sheet rolls. The transmittance of colored plastic sheet rolls depends on the amount and dispersion of pigments. The greater the amount of pigment, the lower the dispersion and the lower the transmittance.
Application: Colored plastic sheet rolls are often used to make food packaging boxes, beverage bottles, cosmetic bottles, toys, etc., because the color can attract consumers’ attention and improve the visual effect of the product. Transparent PET plastic sheet rolls are often used to make food packaging boxes, beverage bottles, electronic product shells, etc., because transparency can show the appearance of the product and improve the grade of the product.
Comparison between colored PET plastic sheet rolls and transparent plastic sheet rolls:
Characteristics | Colored PET plastic sheet rolls | Transparent PET plastic sheet rolls |
Color | Yes | No |
Transmittance | Low | High |
Applications | Food packaging, beverage bottles, cosmetic bottles, toys, etc. | Food packaging, beverage bottles, electronic product shells, etc. |
Advantages | Attract consumer attention and improve product visual effects | Show product appearance and improve product grade |
Disadvantages | Low transmittance | Easy to scratch |
Factors affecting the transmittance of colored PET plastic sheet rolls
The transmittance of colored PET plastic sheet rolls is influenced by several factors, including material properties, manufacturing processes, and environmental conditions. Here are the key factors:
1. Color and Pigmentation
(1) Dye Concentration: Higher concentrations of dyes or pigments reduce transmittance by increasing the opacity of the material.
(2)Type of Pigment: Different pigments have varying effects on light absorption and scattering, which can alter transmittance.
2. Thickness of the Sheet
(1) Increased Thickness: Thicker sheets typically have lower transmittance due to more material for light to pass through, which increases absorption and scattering.
3. Additives
(1) UV Stabilizers: Additives that protect against UV degradation can affect the overall transmittance, especially in the UV spectrum.
(2) Fillers: Additives such as fillers can scatter light and reduce transmittance.
4. Surface Finish
(1) Smooth vs. Textured Surface: Smooth surfaces tend to have higher transmittance compared to textured or matte surfaces, which can scatter light.
5. Crystallinity
(1) Amorphous vs. Crystalline Regions: Higher crystallinity in PET reduces transmittance due to increased light scattering within the crystalline regions.
6. Manufacturing Process
(1) Extrusion and Stretching: The way the PET sheet is extruded and stretched during manufacturing can affect its molecular alignment, impacting transmittance.
(2) Heat Treatment: Thermal processes can influence the degree of crystallinity and the optical properties of the PET plastic sheet rolls.
7. Environmental Factors
(1) Exposure to Light and Heat: Prolonged exposure to light and heat can cause degradation and changes in the transmittance properties of PET plastic sheet rolls.
(2) Moisture: Absorption of moisture can affect the optical properties and clarity of plastic sheet rolls.
8. Contaminants and Impurities
(1) Inclusions: Presence of contaminants or impurities within the PET material can scatter light and reduce transmittance.
By considering these factors, we can control and optimize the transmittance properties of colored PET plastic sheet rolls for various applications.
More Products
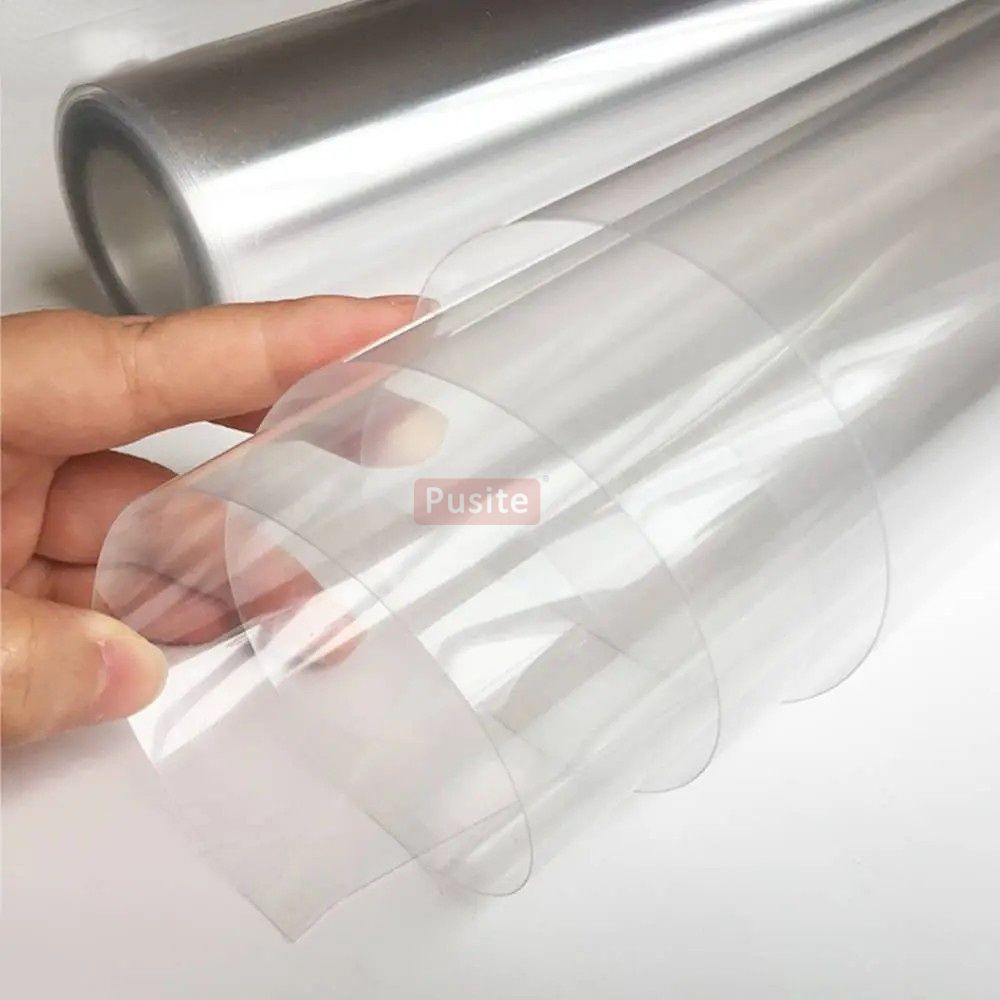
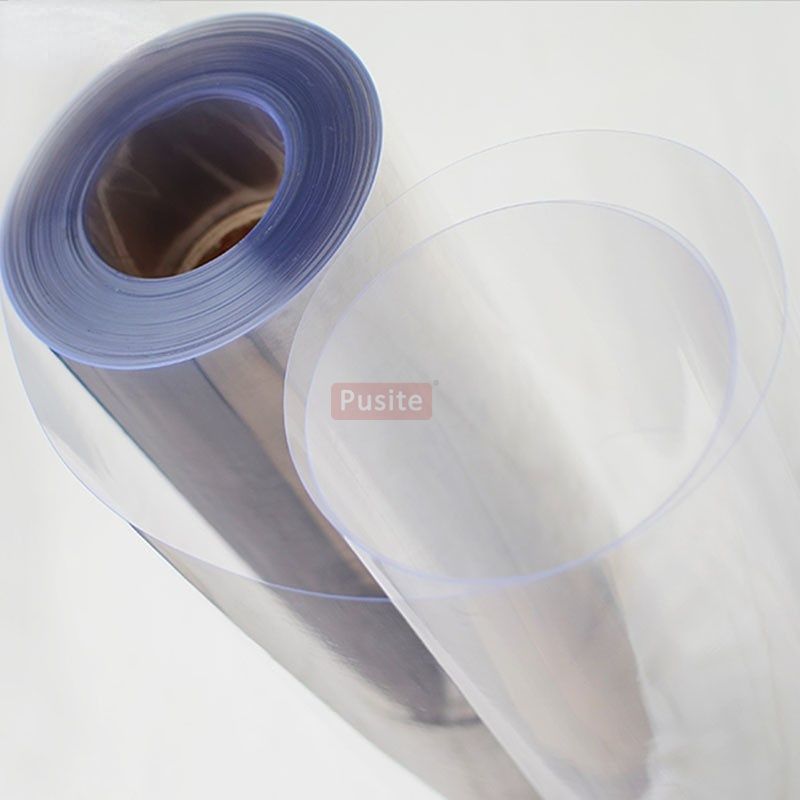
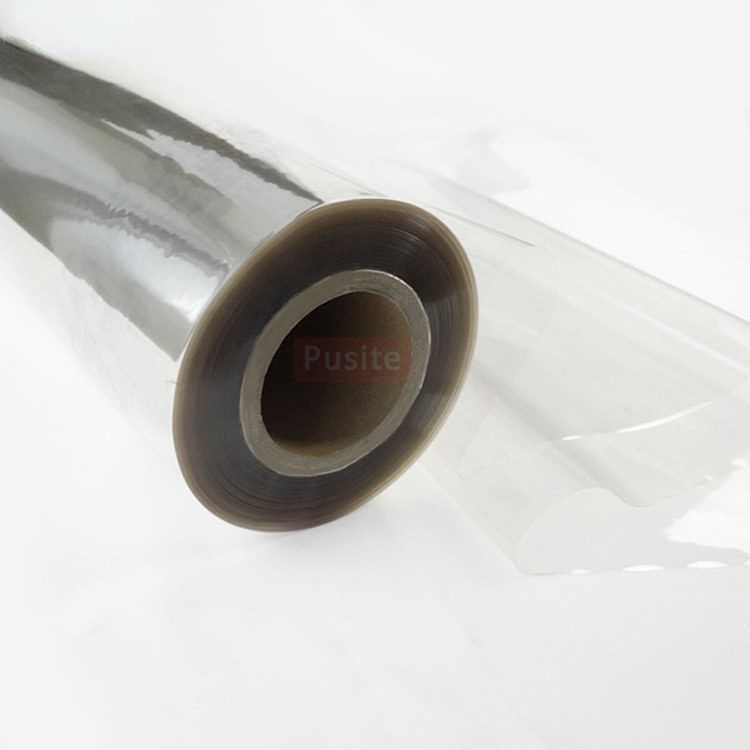
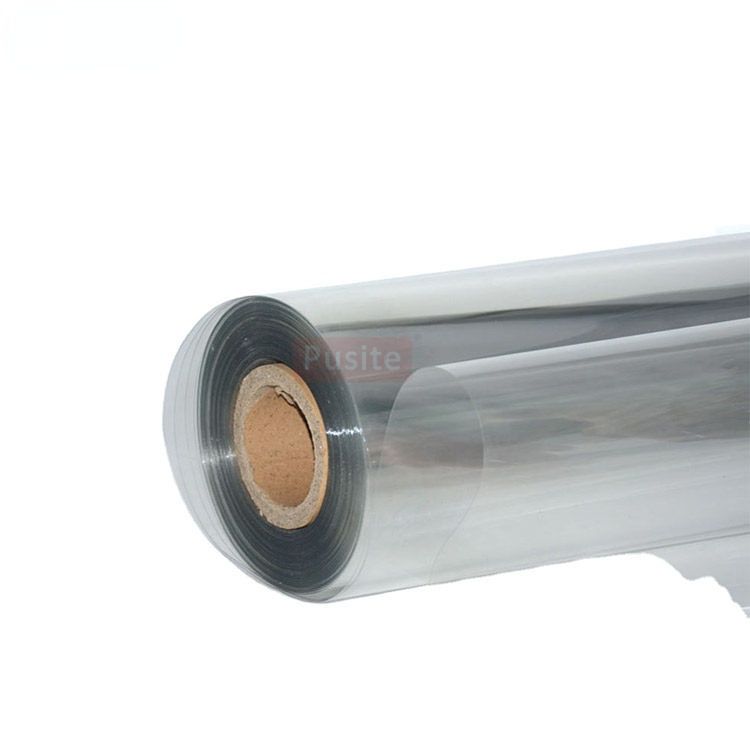
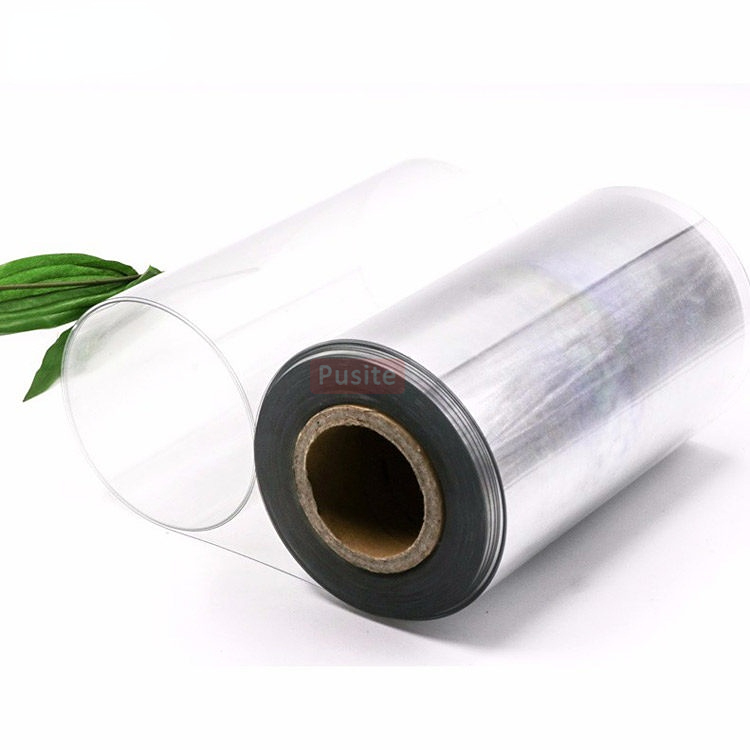
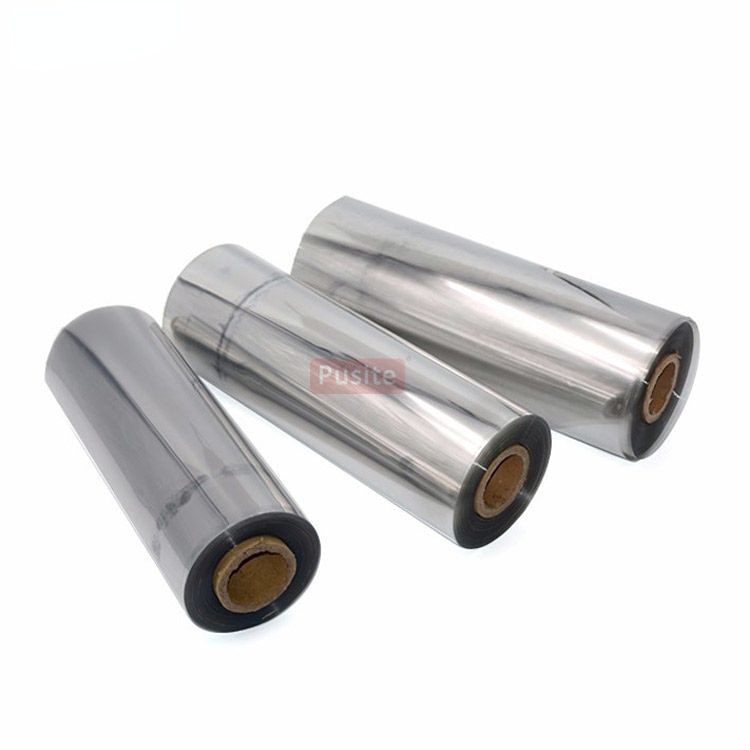