Achieve effect methods of HIPS plastic roll
High impact polystyrene (HIPS) plastic roll antistatic is widely used in electronic product packaging, HIPS plastic roll itself is a non-conductive material. The antistatic effect of HIPS plastic roll can be increased by adding antistatic agent, modifying HIPS resin, etc.
1. Additive Method
Incorporate antistatic additives into the HIPS during the compounding process. These additives migrate to the surface of the plastic, providing a conductive layer that dissipates static charges.
2. Surface Coating
Apply an antistatic coating or spray to the surface of the HIPS rolls. These coatings can be temporary or permanent and are typically applied after the manufacturing process.
Antistatic Sprays: Temporary solution, needs reapplication.
Antistatic Coatings: Permanent or semi-permanent, often used in industrial applications.
3. Conductive Fillers
Incorporate conductive fillers into the HIPS. These fillers create a conductive network within the plastic, helping to dissipate static electricity. Common conductive fillers include: Carbon Black, Carbon Fibers, Carbon Nanotubes.
4. Blending with Conductive Polymers
Blend HIPS with inherently conductive polymers (ICPs) such as polyaniline or polythiophene. This method combines the properties of HIPS with the conductivity of ICPs.
5. External Grounding
Implement grounding methods where the HIPS roll is used. This involves connecting the plastic to a ground source to dissipate static electricity safely.
6. Environmental Control
Control the environmental factors around the HIPS roll. Increasing the humidity in the environment can help reduce static build-up. Humidity control is often used in combination with other methods.
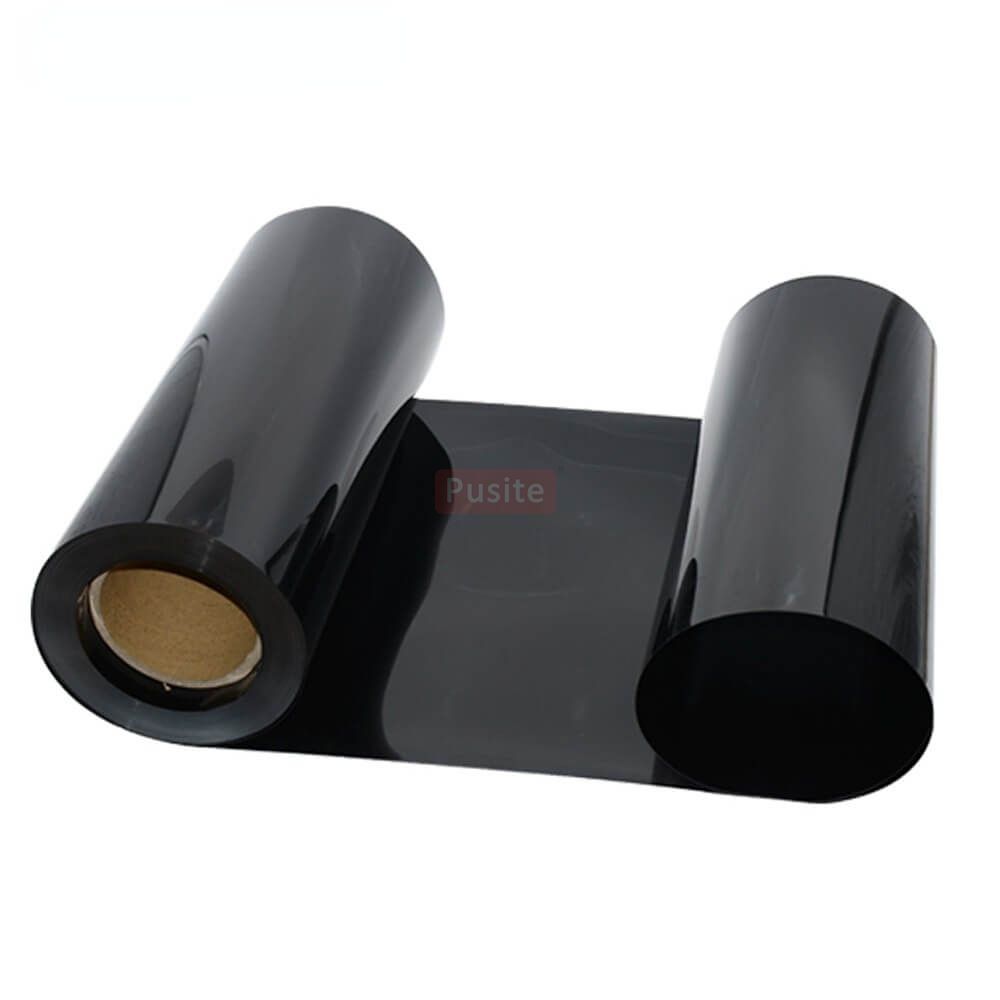
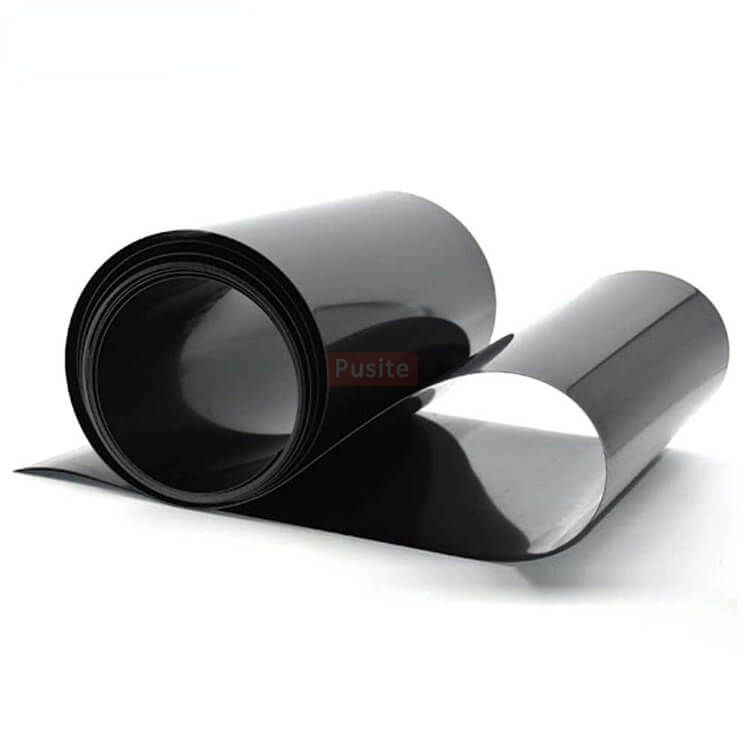
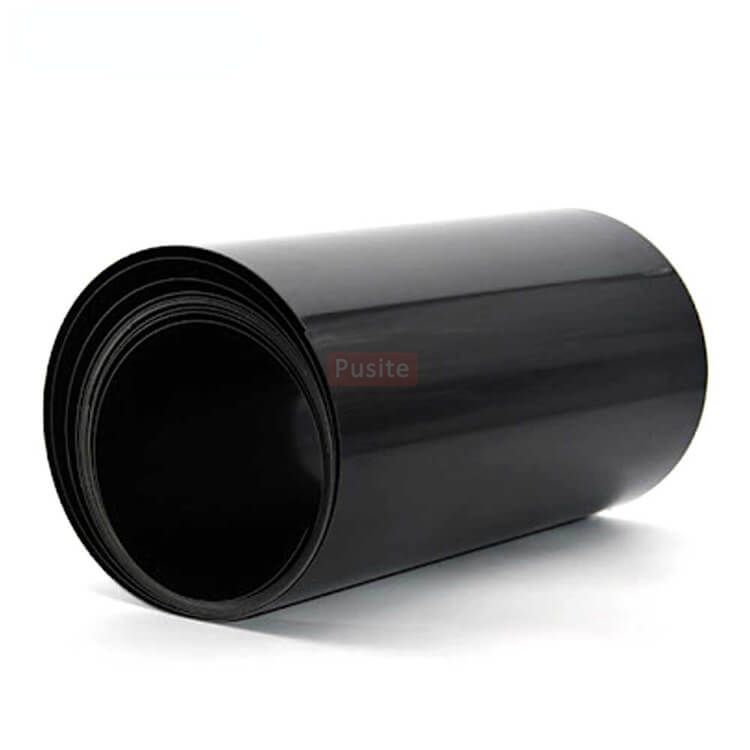
Steps to Apply Antistatic Additives
1. Selection of Additive: Choose the appropriate antistatic additive based on compatibility with HIPS, effectiveness, and desired lifespan of the antistatic property.
2. Compounding: Incorporate the additive into the HIPS resin during the compounding process. This can be done using an extruder.
3. Processing: Process the compounded HIPS resin into rolls using standard extrusion or molding techniques.
4. Testing: Test the antistatic properties of the finished HIPS roll to ensure it meets the required standards. Use surface resistivity or static decay tests.
By integrating one or more of these methods, you can achieve effective antistatic properties in HIPS plastic rolls.
Benefits of making HIPS plastic roll achieve antistatic effect
High Impact Polystyrene (HIPS) is a versatile and cost-effective plastic commonly used in packaging, disposable products, and various industrial applications. Achieving an antistatic effect in HIPS plastic rolls can offer several benefits:
1. Reduced Dust and Particulate Attraction
Antistatic HIPS plastic roll minimizes the attraction of dust and particulates, maintaining cleaner surfaces and improving the quality and appearance of the final product.
2. Improved Safety
By reducing static electricity, the risk of static discharge is minimized, which can prevent sparks that could ignite flammable substances, enhancing workplace safety.
3. Enhanced Process Efficiency
Antistatic properties can reduce sticking and clinging of the plastic during manufacturing and processing, leading to smoother operations, fewer stoppages, and less waste.
4. Better Performance in Electronic Applications
For packaging electronic components, antistatic HIPS prevents static buildup that could potentially damage sensitive electronic parts, ensuring better protection and reliability.
5. Extended Product Life
Reducing static buildup can prevent premature wear and tear on both the HIPS material and the equipment it interacts with, extending the lifespan of both.
6. Improved User Experience
Products made from antistatic HIPS are more user-friendly as they do not cling to hands or clothing and do not attract dust, improving overall handling and appearance.
7. Regulatory Compliance
Certain industries require materials to meet specific antistatic standards. Antistatic HIPS ensures compliance with these regulations, facilitating market access and acceptance.
8. Versatility in Applications
Antistatic HIPS can be used in a wider range of applications, including medical, electronic, and cleanroom environments, where static control is critical.
9. Reduced Maintenance Costs
With less dust and particulate buildup, cleaning and maintenance costs are lowered, as the need for frequent cleaning is reduced.
10. Enhanced Printability and Coating Adherence:
Antistatic properties can improve the adherence of inks and coatings, leading to better-quality printing and finishing on HIPS products.
These benefits highlight the importance of incorporating antistatic properties into HIPS plastic rolls, particularly for industries where static electricity can pose significant challenges.
What is Antistatic HIPS plastic roll ?
Antistatic High Impact Polystyrene (HIPS) plastic roll is a form of HIPS that has been specially treated or formulated to dissipate static electricity. High Impact Polystyrene is known for its toughness, ease of processing, and cost-effectiveness, making it popular in a variety of applications. When HIPS is made antistatic, it gains the ability to prevent the buildup of static electricity on its surface.
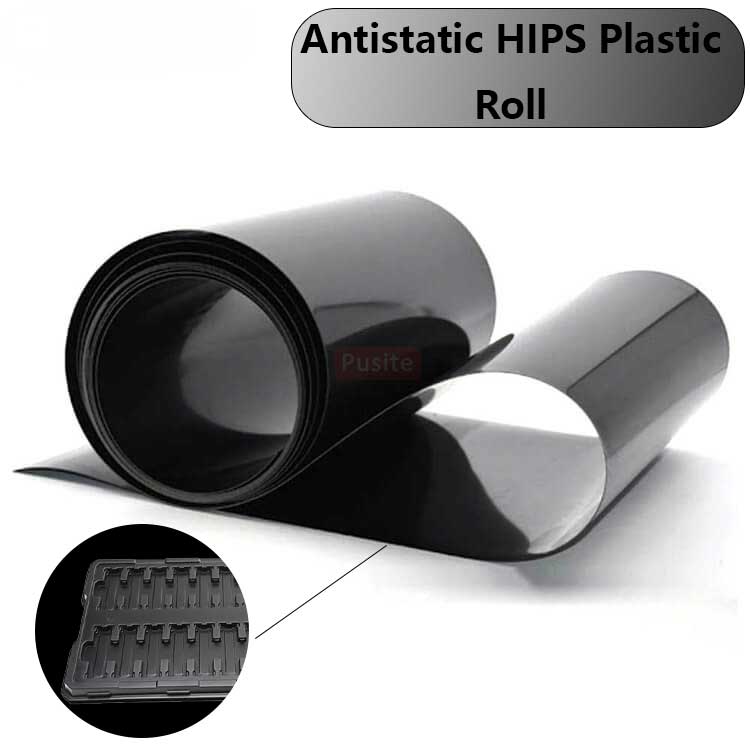
Composition and Production
Base Material: The base material is High Impact Polystyrene, a polymer known for its high impact strength and toughness.
Antistatic Additives: Antistatic HIPS is produced by incorporating antistatic additives into the polymer matrix. These additives can be external coatings applied to the surface or internal additives mixed into the polymer during the production process.
Common antistatic agents include surfactants, conductive polymers, and carbon-based additives.
Properties
Static Dissipation: The primary feature is its ability to dissipate static electricity, preventing the buildup of static charges on its surface. This is typically achieved by allowing charges to migrate across the surface or through the material to a grounding point.
Maintained Mechanical Properties: Antistatic HIPS retains the advantageous properties of standard HIPS, such as impact resistance, durability, and ease of thermoforming.
Surface Resistivity: Antistatic HIPS has a lower surface resistivity compared to standard HIPS, which helps in reducing static buildup.
Applications
Packaging: Used for packaging electronic components to prevent electrostatic discharge (ESD) damage.
Food and medical packaging where cleanliness and reduced particulate attraction are crucial.
Industrial Uses: Used in environments where dust and particulate control is important, such as cleanrooms.
Material handling trays, bins, and containers in manufacturing settings.
Consumer Products: Used in products that benefit from reduced static cling, such as certain types of office supplies and household items.
Electronics: Widely used in the electronics industry for cases, enclosures, and protective packaging of electronic devices and components.
Pusite can offer- Antistatic HIPS plastic roll
Item | Antistatic HIPS plastic roll, High Impact Polystyrene Sheet Roll, HIPS Plastic Sheet, Rgid HIPS Film |
Brand | Pusite |
Origin | Shanghai, China |
Width | 300~850mm |
Thickness | 0.2~2.0mm |
Weight | 50-150kg/roll |
Shape | Roll/Sheet |
Material | 100% virgin |
Color | Black, White, Color, Natural, Translucent. |
Performance | Conductive, Antistatic, EOVH High barrier |
Surface treatment | Matte, high gloss, flocking, etc. |
Material | Surface resistance (Ω/sq) | Characteristic |
Conductive | 103 to 105 | Conductive materials have low resistance, so electrons can easily flow through the surface or inside of these materials. The charge will flow to the ground or another conductive object in contact with the material. |
Static dissipation | 105 to 109 | Compared with conductive materials, static dissipative materials can make charge flow to the ground or other conductors in a more controlled and slow manner. |
Anti-static | 109 to 1012 | Anti-static materials can inhibit friction and electricity generation. |